Design Guide for 3D Printing
The 3D Printing Design Guide is for anyone interested in 3D printing. In this guide we will explain the basic principles to consider when modeling the print part.
This guide will cover the essential basic concepts that must be understood within the print design part process. Although all printing technology has unique limitations and conditions in production, there are valid principles in all print technologies.
When designing a three-dimensional printable model, keep in mind that the computerized model will become a physical model.
While the digital environment does not have physical laws and basically allows the creation of just about anything, the laws of physics will apply to the physical model and therefore not everything designed in computer software will be printable.
In our printer technology pages ( SLS , MJF , SLA , FDM , POLYJET , SANDSTONE ) are the design-specific principles for each printer.
Ready to begin?
Guidelines for 3D Printing
Characterization of the desired product in advance
In order to be able to print models in the best possible way, one must first understand primarily the needs of the model, its features, its geometry and the conditions it needs to meet. Only when the desired product is well-characterized and well-defined can you proceed to find the technology most suitable for printing. A recommended way to characterize the desired product is to write its final features in order of importance. Depending on the priorities of the part features, technology should be sought to enable the manufacturing to meet the most important features of the product.
Choosing the technology to manufacture - Know the limitations of the printer
3D printing technologies differ from one another and their production limits vary according to technology, print material, and printed product. Each technology has its advantages and disadvantages. Once we have defined and characterized the properties of the printed product, we must look for technology whose benefits will be used to create an optimal product.
Parts design for 3D printing in different technologies varies depending on printer conditions and raw material. There are now a number of key design considerations that should be taken into consideration in accordance with the technology chosen.
Limitations of printed matter
3D printers of various types usually allow printing in a variety of materials. Printer features and parts printing results when printing one material are generally not the same as printing on the same printer with another material. In order to design an optimal part for 3D printing, the properties of the material from which the part will be printed are well known. For example, designing ultra-thin, ultra-thin sections for crisp, easy-to-break printing will create a gap between the properties of the printed material and the desired part.
In addition, there are sometimes differences between the results of different printers that print the same raw material. Nylon 12 (PA12) for example, is a raw material used by both the PROX500 and the FusionJet4200. However, the same parts printed on the same raw material on different printers will behave slightly differently from one another. Another example is PLA (plastic) raw material widely used in FDM technologies may behave differently when printing on a MAKERBOT printer and printing on another printer.
Basic terms
Watertightness
3D printable files are mesh files. Common files are 3D files where the model consists of a network of triangles connected to each other, these triangles are called polygons. Also files that are modeled in software that does not produce silk files are converted prior to the printing process to silk files composed of a polygon network. In order for a model to be printable, the polygons network must be continuous, with no spaces, holes, missing polygons and openings.
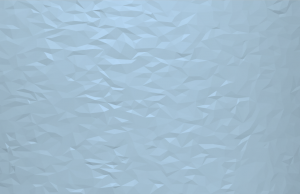
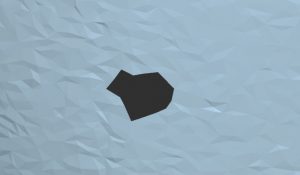
To illustrate, a model that is closed and continuous can be simulated into balloons of various shapes that capture air within them. A model containing a certain type of hole is not printable like a stencil with a hole is not an inflated balloon. In English, the description for a closed model is Watertight, much like an air-trapping balloon without being able to exit, so the description “Watertight” – “waterproof” means a water product cannot penetrate or exit it and hence it is closed, missing holes or spaces between surfaces. Note that it is important that the polygons that make up the model are continuous but do not mean open spaces in the model similar to the inner space of a ring.
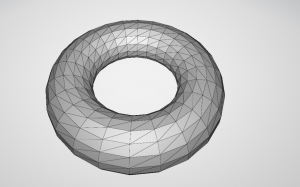
A file that can be printed even though there is an “open space” in its center – the file is Watertight because its polygon network is continuous and has no holes.
There is a wide variety of software in which to make sure the model is without holes before sending for printing. The IMPACT LABS 3D printing system performs polygon discontinuity testing or holes and alerts the user if there are holes in his model.
Thickness
3D printers allow production of a variety of materials and technologies, each material and technology has different wall thickness limitations. There are technologies where printing too thin a model will distort the model, and other technologies creating too thin a model can cause the model to break. Therefore, the limitations of the technology used are checked.
In addition, the geometry of the model is of great influence. Two models made of the same wall thickness with the same technology but with different geometries will respond differently to distortions and degree of breakage. For example, usually large, thin surfaces will be more likely to warp.
The optimum wall thickness for the model varies according to the geometry and can vary between different parts of the model. Different edges in the model require a different minimum thickness that varies according to their support by other edges.
Details size
When the printed model contains small details, note the size of the details that the selected technology can produce. The size of the details is selected from the accuracy of the printer and the thickness of the printed layer. In addition, the size of the details is also affected by the printed material, in some materials small details may distort, while in other materials small details may erode or break.
Holes rods
Holes are another type of submerged detail. Note the depth of the hole and its diameter that can be created in any technology. In addition, it should be noted whether the hole can be cleaned from conventional material.
Rods are prominent details of the surface with a narrow, high geometry. Such thin details have a tendency to break or warp and therefore the pole height should be noted with respect to its diameter.
Enclosed spaces Diameter drilled Minimum cleaning
There are printable models whose geometry contains enclosed spaces that capture printed material that does not undergo a hardening process or capture various types of supports. Different printing technologies fill the enclosed space in different ways to support the walls that capture the space.
There are technologies in which such internal spaces can create pressures within the model and cause distortion. In addition, the material trapped inside the enclosed space adds to the weight of the model.
In order to get the material out of space and to avoid too much effort on the sides of the model, a small hole can be made through which the material came out at the end of printing.
Hole diameter and need varies from technology to technology.
Resolution
In order to select the designed part resolution for 3D printing, the resolution limits of each printer and raw material must be known specifically. A high-resolution, unattainable part design in print technology anyway creates an unnecessarily large and heavy file that can delay print time without improving final product. The resolution that meets the desired product requirements must be selected and can be printed using the selected technology but no more.
Space between moving parts CLEARANCE
Printing a number of components that work together as one system that enables movement requires further deepening of the selected technology features. The required space between two interconnected parts that allows them to produce a variable active mechanism according to the chosen technology.
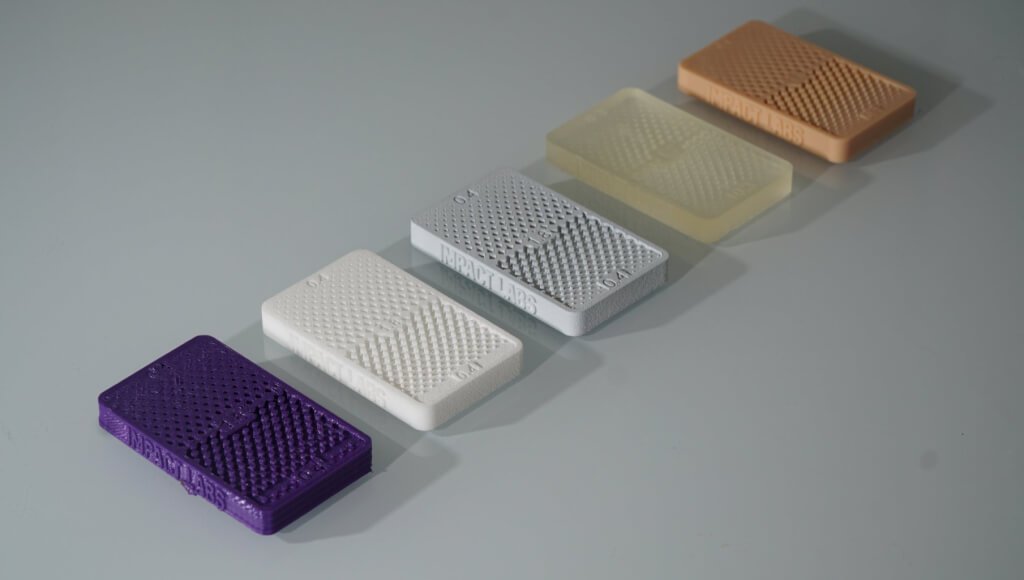
In summary, there are a variety of considerations to consider when planing and designing parts manufactured in 3D printing. At times, the amount of conditions affecting the model design for 3D printing can be confusing. At IMPACT LABS we are willing to walk you through the plan and design process of your 3D printing model best.
IMPACT LABS has a team of expert engineers and designers together with technology hubs that provide a variety of services ranging from consulting on the best technology for producing the best product for you to designing print models based on your idea. Our main advantage is that we also plan and design for printers and also operate the printers ourselves, so we know each technology closely and operate while efficiently and saving time and money for our customers.
The IMPACT LABS team of experts accompanies production processes at any stage of your choice – from concept development, product design phase to the optimal technology selection stages and product production ideally.